Sink or Swim? Why Today’s Supply Chain Matters More Than Ever.
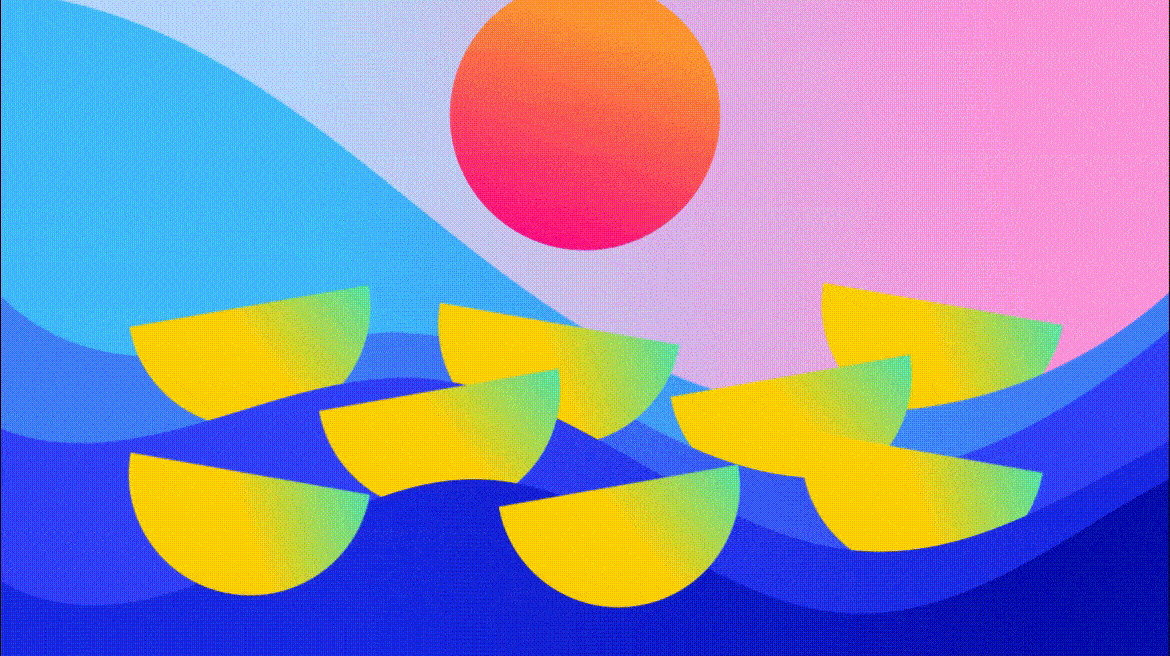
If you’ve been in a grocery store recently, you’ve probably noticed the empty shelves, items out of stock or an imposed limit on how much of an item one can buy (toilet paper, anyone?). If you’re a business, chances are you’ve heard or experienced the horror stories about cargo “lost at sea.” Just about every person has felt the effects of the disrupted supply chain in one way or another.
When the supply chain runs well, we don’t think about it. But when there are issues or delays, it affects everything that powers our everyday lives, from the semiconductors (chips) in our smartphones to couch deliveries to medicines. The current supply chain is always at constant risk of systemic failure.
Supply chain leaders must holistically rethink the supply chain to build more resilience and prevent a similar situation in the future. A noticeable trend among supply chain leaders is moving from a reactive system to a more proactive one, which is long overdue. No longer are real-time analytics seen as useful, they want real-time actionable options instead. Inventories and product journeys can no longer depend on old methods. All while moving to a more regional supply chain strategy, where product gets transported within the same continent instead of depending on overseas shipping.
Many supply chain logistic industry leaders have focused on “real-time” as the number one feature for their End-to-End visibility (E2E) offerings. What they mean by E2E is having access to the exact location of where their product is at all times, how it’s doing, what it’s facing, and predictions as to how it might arrive up until the point that it’s given to the end customer. Yet, what many of these leaders learned was that knowing what was happening in real time versus acting in real time held very different values. Just knowing their product suffered a temperature deviation while still sitting on a ship thousands of miles from its destination is not enough. They’d rather be able to predict excursions that may happen and create risk-prevention measures to stop them from happening.
But why did supply chain leaders switch to needing real time action over real-time visibility?
The supply chain is a transportation network between a company and its suppliers for distributing goods or services that can span several checkpoints, such as land, sea and air. All stakeholders involved use their own tracking systems, which for many is still done manually. For years, the supply chain has worked on a “just-in-time” system, meaning there are just enough products for the current demand. But when there are delays in the supply chain, the just-in-time system doesn’t work as well and inventory often falls short. It is then more likely that shelves will be empty when there are delays in the supply chain–which is what we’re experiencing now. An estimated 60% of Americans surveyed by Gallup reported they have been unable to buy a product due to supply chain disruptions.
As we’ve seen over the last few years, governments and corporations responded to COVID-19 with shutdowns or capacity restrictions, causing widespread disturbance. For example, China’s response to COVID-19 has had a significant global impact. Back in January of 2020, China went into COVID-19 lockdown and factories were forced to slow production. China’s limited production led to a 7% drop in imports for affected firms. Early this year, China tightened their measures on cold chain shipping of medicines and foods to stop further spread, while a spike in consumer demand led to bottlenecks at California ports. The Wall Street Journal reported that the number of ships queuing to enter California ports declined to 78 vessels in February, down from the peak of 109 vessels typically waiting to enter the ports. It is making a slow recovery, but continuing to create shortages in many industries like technology and automotive. All this disruption was the result of only one country’s restrictions, and will likely continue as China entered another lockdown period just weeks ago.
The real question here is how this will affect the general population. Food prices surged by 7% and energy prices have risen 27% since the start of the year. More people will be unable to buy the food they need to support themselves and their families, which will lead to more food insecurity. The Consumer Price Index from the Bureau of Labor Statistics indicates that inflation has reached a 40-year high of 7.5%, forcing people to adjust their budgets and start buying less due to the rising prices. On top of that, there will be another domino effect with less money circulating in the economy.
Retail and consumer goods aren’t the only industries raising prices. Restaurants also have to raise their prices just to stay open. And it’s not just because of food. The shortage of plastics and aluminum are also having an impact. A restaurant in Texas called Wings N’ More said they have had to raise their prices by 12%, and may have to raise them more as the cost of paper and plastics have since increased between 200%-300%.
Pharmaceutical transport is another industry heavily affected by this disruption. Difficulties shipping medicines mean that those who need them most no longer have access. According to physicians in an Ipsos poll, 4 out of 5 physicians faced a medicine shortage at their facilities in 2021. When medicines that need to be temperature controlled sit in shipping containers for too long, they can’t be sold because of liability issues. Typically, supply chain quality assurance teams need at least two weeks to investigate the product and how long it suffered temperature deviation before it can be released to the public. This, along with the extended time it takes for medicines to get to stores, will lead to a medicine shortage and increased prices. This happened early in the pandemic, where prices for 832 drugs had risen an average 4.5% in January 2021 from the previous year, according to GoodRX. Many people who need these medicines won’t be able to find them, especially in underserved communities. According to the Ipsos poll, 37% of physicians who worked in underserved areas said the drug shortage has led to poor patient outcomes, compared to 29% of physicians in more resourced areas and add to the domino effect.
Food shortages and semiconductor shortages, among others, are expected to persist into summer, continuing to affect both businesses and consumers alike. To combat this, companies need to rethink their supply chains and give their E2E visibility solutions a full makeover. Some have started to automate parts of their supply chain to keep up with demand and fill the labor gap. For example, Nike installed over 1,000 robots to help ship orders from its distribution centers. The automation of their distribution has helped triple the digital order capacity. Imagine how many more products could move through the supply chain with more automation. Imagine if that was food or medicine.
Additionally, the Great Resignation of 2021 led to less people working in distribution centers, causing a slow recovery for the supply chain. Forbes reported that manufacturing employment dipped by nearly 400,000 from pre-pandemic levels. With fewer warehouse employees, either from resignations or the effects of COVID-19, the supply chain slowed, adding to the neverending problem. However, the use of automated systems has the ability to help solve this, as delays from slow-moving distribution centers could be predicted and leaders could make decisions quickly to minimize delays.
Along with automation, another necessary change is a switch from a “demand chain” or “just-in-case” system which will help supply chain resilience. A demand chain means that efforts are focused mostly on what consumers are demanding. More attention on items with high demand will ensure that they move faster through the supply chain. A just-in-case system would prevent shortages of products because there is a surplus of product to rely on when the supply chain isn’t efficient. Then, automation can be used again to keep track of inventory and ordering trends that can provide risk analysis to those in charge of supply.
Another solution is less reliance on global imports and exports, and more support through domestic manufacturing. Producing more in the US could greatly help our supply chain. With less reliance on other countries, there would be less shortages experienced quarterly or even annually. According to physicians in an Ipsos poll, 90% think that the US needs to produce more medicines as reliance on other countries for medicine is cited as the top contributor to medicine shortages in the US. Tech companies have already started to invest in factories in the US. In November, Samsung invested $17 billion into a semiconductor plant in Texas. This would allow for more semiconductors to be produced and move faster through the supply chain especially because supply chains are taking a more regional approach, a lesson learned from the pandemic. Ultimately, there would be less of a wait time for semiconductors so more automotive and technology products can be produced. Therefore, the manufacturing of products in the US would greatly ease our reliance on other countries and allow us to receive necessary goods in a timely and effective manner.
Unfortunately, the supply chain crisis won’t be ending this year and many of our favorite products will likely experience shortages and unusually high prices. Items in high demand like semiconductors or summer food favorites will be low in supply and high in price. We are still navigating the pandemic and feeling the effects of early COVID-19 restrictions even as the rest of the world unmasks.
If one thing is clear, it is that for far too long we have relied on a weak, and often manual, supply chain that is ripe for innovation and in need of immediate change. Supply chain disruptions now clearly affect our daily lives, and continuous disruptions will have a much larger impact on our future business infrastructure. Especially as everyday e-commerce continues to grow and even surpass what we might normally have considered “Christmas-level” demand. Businesses will have to rethink how they use the supply chain and how to leverage the predicted trends to work for them, as supply chain leaders, rather than against them.
These supply chain challenges have made our work as a demand design consultancy even more vital, as we’ve been able to use our unique perspective of partnering with both global brands and supply chain leaders to help explore forward-looking ways to drive growth for their businesses in light of all of this – whether it’s through smarter marketing strategies or helping them undertake full digital business model innovation.
Thinking about how you can navigate your current or future supply chain issues? We’ve got a speedboat ready to help you chart your next course forward.